
HW
CHANGE:WATER LABS FIRST ITERATION PROTOTYPE
A colleague and I constructed the structural prototype for change:WATER Labs' first rough product iteration. This serves as structural support for a proof-of-concept test, to see how the polymer membrane--shaped in the chemical lab--performs at a full size scale. At my internship position at this startup out of MIT's D-Lab and Legatum Center, I am tasked with all the structural, support, attachment, force analysis, modelling, ventilation and desiccation systems of the product--in other words, what the user sees, how they use it, how they interact with it, and some functional elements to aid in the rate of the main chemical process inside.
​
The product is a non-sewered, waterless toilet to address unhealthy sanitation for the urban poor, and to greatly reduce open defecation, unsafe conditions for women, inadequate servicing, and overwhelmed utilities with a cheap and passive technology. It utilizes a polymer membrane that pervaporates pure water from raw waste without using energy, reducing waste volume by 95%. For more information about what change:WATER Labs is doing, click here.
​
There were two main tracks in prototype design that we are developing hand-in-hand.
One is the typical user-centered design process in developing the toilet design, which begins with research of customer needs. I learned a lot about climate patterns in the middle east, Hopi Indian reservation sanitation conditions, National Parks Service waste policy, refugee politics and displacement, popup housing, and middle eastern cultural perceptions about toilets and latrines--in other words, the research was thorough. Then, we started our ideation process--how do we want the toilet to look? How much user interaction is necessary? How can we bring manufacturing costs down? How can we integrate and attach the membrane with the toilet structure? How can we avoid cultural taboos in our design? How do we make is natural and seamless to use, without sacrificing functionality (this was a more involved question than I expected, as many systems to increase pervaporation rate were simply not intuitive, or made the process complicated. For instance, high powered ventilation without using extra energy might involve user input. So does urine diversion, a common method in composting toilets). By the end, I developed several diagrams to guide us in our process.
​​


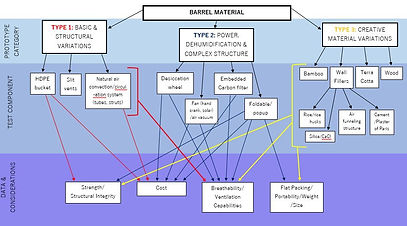
With no shortage of diagrams and CAD models of course.
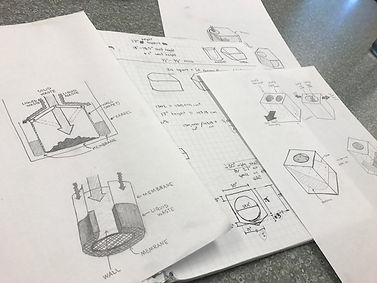
However, our design process needed to work in conjunction with rapid prototyping and testing, since many of these ideas were novel and were not guaranteed to be ideal. We set up five "mini toilets", or closed bucket environments to test various possible ventilation elements for our design. I designed, built and coded sensors with Arduino to gather and upload climate data inside each mini toilet, a hardier variation of which the company will use in its field trials with customers. The data is currently being processed (picture on the left).
​
Secondly, we built a basic proof of concept, made with hardware store materials. This was used in the chemical lab to test the membrane's structural integrity and function on a half size scale. It had to be able to be sat on, and be able to hold the membrane hanging from the top without too much strain on any one part of the membrane (picture on the right).
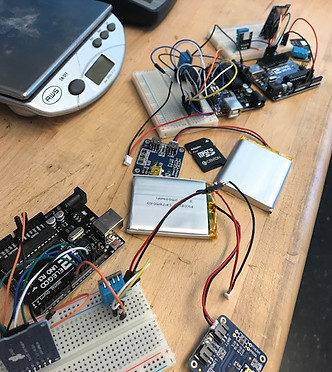

Testing is still in progress, and updates will happen accordingly.